PLC intelligent synchronous lifting and controlling system
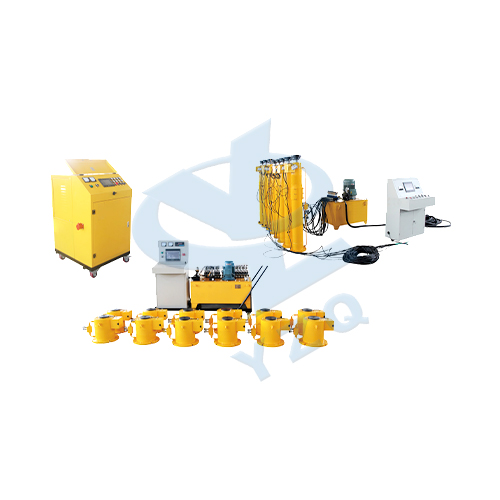
PLC intelligent synchronous lifting control system can be designed according to customer’s request to be controlling 4, 8, 16, 24, 32 or 64or 128 points synchronous lifting system. This project adopts double acting or single acting hydraulic cylinders, supply oil from pump station, goes through over flow valves, then, goes three-position four-way directional valve, and into the cylinders through electromagnetic ball valve. Control going up and down via three-position four-way directional valve, adjust speed of going up and down via switch on or off electromagnetic ball valve which is judged by the signal from displacement sensor to PLC control system, ensure the synchronism of cylinders. Fix hydraulic control single valve on outlet port of the cylinder to keep pressure when it reaches the lifting position, avoid the cylinder fall back. Fix adjustable overflow valve on the return oil line of cylinder to control the speed of going down, avoid fall back with too fast speed in case with big loading.
The theory is setting up PLC computer via operate interface according to the data from displacement sensor and pressure sensor, so, PLC computer operates electric hydraulic pump station and cylinders automatically to lift or location various large or heavy objects, it’ssuitable very much for the heavy object with uneven weight distributions.
●Can set up the numbers of cylinders, PLC computer controls cylinder pressure, stroke, loading etc.
●Working tonnage of each lift point can choose from 5 T to 2000T.
●The Max. and Min. displacement accuracy is ±0.5- 1mm.
●The Max. and Min. pressure accuracy is ±0.5- 1MPa.
●PLC computer control unit works with touch screen accurately. Shows data:
●displacement, Max. and Min. pressure, average value etc.
●Pressure (loading) and displacement alarm improve the safety for lifting heavy object.
●Hydraulic cylinder can be set separately, so it can goes up and downseparately,
●There are devices of pressure maintaining and overflow to avoid overloading. And there is safety valve to ensure safe operations and protect the heavy object.
● Pressure maintaining device is suitable for the occasions where requests maintaining pressure, such as putting girder during bridge construction.
1、Electric hydraulic pump station
2、Touch screen and PLC controller.
3、Double acting or single acting hydraulic cylinder
4、Displacement sensor
5、High pressure hose
6、Cable of displacement sensor
7、Pressure sensor
Normally, PLC synchronous lifting system has six components
electric hydraulic pump station,PLC computer control system,hydraulic cylinders,displacement sensor,human computer operation interface .This system units hydraulic lifting system,computer PLC signal treatment,displacement monitor and pressure monitor, and developed on the united system. Its core is basic on bridge organization analysis and construction methods summary, treat hydraulic system according to computer PLC signal which is designed by bridge characters, enter displacement and pressure single of external monitor equipments, PLC control hydraulic cylinder to left, because of small stroke of thin cylinder, its accuracy error no mare than ±0.5mm, and the accuracy error is no more than ±1mm for long stroke cylinders, lifting range: 50-2000 ton,jacking height:10-2000mm.
Can operate and control the jacking position and load.
Displacement & pressure sensors of hydraulic cylinder ensure high reliability during bad working environments.
Synchronizing loads and overload protect functions avoid expanding cylinder.
Advanced displacement and load synchrony jacking control system is not only achieve high precision synchrony when going up,but also ensure high precision synchrony while going down.
Easy and intuitive operation can finish various complicated works.
Can fix touch screen to show jacking displacement and loading and average data,or fix working condition machine to record the whole construction process.
Can expand to 32 points and more points to be synchrony.During multipoints working,except all points aresynchrony,also can adjust load distributions of every point according to user's requirements.
Product Use:
PLC intelligent synchronous lifting control system can be used widely in bridge synchrony jacking, bridge bearing changing, heighten or reinforce bridge, steel structure entire jacking, construction synchrony translating,grid structure,pile foundation underpining etc.
Using occasions of PLC synchrony jacking system
● Jack bridge.
● Change bridge bearing.
● Tunnel pushing (pipe jacking).
● Adjust heavy equipment.
● Jack body of boat.
● Jack construction, translate existing construction.
● Jack or weight channel of oil well.
● Synchrony pressure machine, translate load horizontally.
● Synchrony jacking net rack.
● Pile foundatuion underpinning.